تفاوت دستگاه های تزریق پلاستیک
معرفی انواع دستگاه تزریق پلاستیک و کاربرد آنها
یکی از پرمصرف ترین، راحت ترین و مهم ترین روشها برای شکل دادن به پلیمر، استفاده از دستگاه تزریق پلاستیک است. بسیاری از وسایل پلاستیکی که در اطراف خود مشاهده میکنید، با استفاده از روش تزریق پلاستیک ساخته شدهاند. دستگاههای تزریق پلاستیک به طور معمول دارای انواع مختلفی هستند و هر کدام از آنها نیز عملکرد متفاوتی دارند. از این رو برای شناخت دقیق این دستگاه و آشنایی با نحوه کارکرد آن خصوصا در خط تولید نایلون توصیه میکنیم تا پایان این مقاله همراه ما بمانید و مطالب مهم را با دقت دنبال کنید.
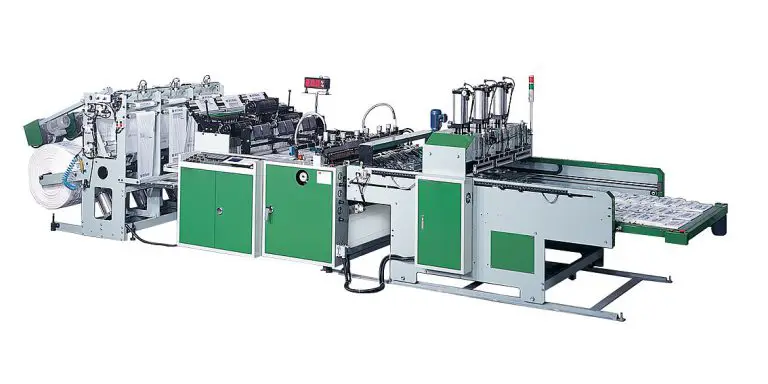
کاربرد دستگاه تزریق پلاستیک
تزریق پلاستیک سادهترین روش تولید محصولات پلاستیکی است که در آن مواد اولیه محصولات پلیمری یا همان پلاستیک به صورت دانههای ریز گرانول وارد دستگاه پلاستیک سازی میشوند. سپس مواد از درون بخشی از دستگاه که به فرم یک لوله است و سیلندر نامیده میشود عبور میکنند. در اطراف سیلندر هیترهایی قرار گرفتهاند که با ایجاد گرما به ذوب مواد پلاستیکی کمک میکنند، اگرچه عمده گرمای مورد نیاز برای ذوب مواد به وسیله نیروی برشی و اصطکاک ماردون تامین میشود که با گردش خود مواد را در طول سیلندر به جلو رانده و متراکم میکند.
مواد مذاب پس از رسیدن به انتهای سیلندر به حالت مذاب یا خمیری شکل در می آیند، در این مرحله مواد به وسیله جکهای هیدرولیکی به درون حفرههای قالب تزریق پلاستیک، تزریق میشوند. کانالهایی برای گردش آب سرد در اطراف حفرههای قالب وجود دارد تا از این طریق مواد در قالب منجمد شده و به فرم نهایی خود برسند. حال که با روش تزریق پلاستیک به اختصار آشنا شدید، بهتر است با کاربرد دستگاه تزریق پلاستیک نیز آشنا شوید.
همان طور که در ابتدای مقاله نیز گفته شد استفاده از دستگاههای تزریق پلاستیک کاربردهای گوناگونی دارد و امروزه به طور گستردهای در تولید قطعات پلاستیکی مورد استفاده میگیرند. تولید ظروف پلاستیکی، درب بطری، سبد میوه، لوازم خانگی، تجهیزات پزشکی، و انواع لوازم یکبار مصرف پلاستیکی تنها گوشهای از کاربردهای این دستگاه به شمار میروند.
بسیاری از قطعات خودرو مانند قاب آینه، سپر، جا لیوانی، داشبورد و عمده تزئینات داخلی خودرو نیز با استفاده از دستگاههای تزریق پلاستیک تولید میشوند. دستگاه تزریق پلاستیک در تولید تجهیزات پزشکی هم نقش مهمی دارد.
بسیاری از لوازم یکبار مصرف آزمایشگاهی مانند لوله خون، انواع ظروف نمونه گیری، لوله سانتریفیوژ، سر پیپت یا سر سمپلر و همچنین گستره وسیعی از تجهیزات پزشکی مانند بسیاری از قطعات انواع ماسک اکسیژن، ستهای تنفسی، ستهای بیهوشی، انواع سرنگ، قلم انسولین، آنژیوکت و پمپ درد با استفاده از دستگاه تزریق پلاستیک تولید میشوند.
دستگاه تزریق پلاستیک در تولید بسیاری از محصولات نقشی کلیدی دارد، به طور مثال صنایع تولید لوازم خانگی، لوازم کشاورزی و باغبانی، اسباب بازی، لوازم ساختمانی، قطعات نظامی، قطعات هواپیما، تجهیزات مخابراتی، لوازم برقی، کامپیوتر و تلفن همراه تنها گوشه ای از صنایعی به شمار میروند که وابستگی انکار ناپذیری به تزریق پلاستیک دارند.
همان طور که متوجه شدید کاربرد دستگاه تزریق پلاستیک بسیار متنوع بوده و در زمینههای مختلفی میتوان از آن بهره گرفت. گستره وسیع و تنوع کاربردهای دستگاه تزریق پلاستیک باعث شده است تا این دستگاه در انواع و اقسام گوناگونی ساخته شود، در ادامه با مهمترین انواع دستگاه تزریق آشنا خواهیم شد.
انواع دستگاه تزریق پلاستیک
به طور کلی دستگاههای تزریق پلاستیک از نظر سیستم تولید و انتقال قدرت در 3 دسته، هیدرولیکی، تمام برقی و هیبریدی قابل تقسیم میشوند.
دستگاه تزریق پلاستیک هیدرولیکی
دستگاه تزریق پلاستیک هیدرولیکی پر کاربردترین نوع دستگاه تزریق پلاستیک به شمار میرود و کاربردهای بسیار وسیعی دارد. حرکتهای خطی رفت و برگشتی مانند باز و بسته شدن گیره در این دستگاه توسط جکهای هیدرولیک و حرکات دورانی مانند بارگیری با استفاده از هیدروموتور انجام میشوند. مهمترین مزایای دستگاههای تزریق هیدرولیکی قدرت بسیار بالا و قیمت ارزانتر آنها است. جریان روغن هیدرولیک در این نوع از دستگاههای تزریق پلاستیک توسط انواع پمپهای هیدرولیک جابجایی مثبت مانند پمپهای دندهای، پیستونی یا پرهای تامین میشود. نیروی مورد نیاز برای گردش پمپ نیز توسط موتورهای الکتریکی القایی یا موتورهای سروو تامین می شود.
مزایای دستگاه تزریق پلاستیک هیدرولیکی:
برخی از مزایای دستگاههای تزریق پلاستیک هیدرولیکی نسبت به دستگاههای تمام برقی عبارتند از:
- نیروی قفل گیره بیشتر برای قطعات بزرگ
- نرخ تزریق بهتر
- مقاومت بالا نسبت به سایش و گسیختگی
- حجم تزریق بیشتر
- توانایی پران بهتر
- توانایی استفاده از آکومولاتور جهت کنترل سرعت گیره
- هزینه اولیه خرید پایین
- کم هزینه و در دسترس بودن قطعات یدکی آن
- سهولت در استفاده برای پروژههای سطح بالا
- وجود بسیاری از قطعات آن در بازار دست دوم به دلیل محبوبیت و فراوانی این دستگاهها
نقاط ضعف دستگاه تزریق پلاستیک هیدرولیکی:
بدلیل قدرت بالای این دستگاهها، مصرف انرژی دستگاههای هیدرولیکی در حالت ایدهآل نیز بالا است. در حالیکه یک دستگاه برقی معمولی میتواند مصرف انرژی معادل 2.55kWh در زمان تزریق داشته باشد، دستگاه تزریق هیدرولیکی ممکن است مصرفی برابر 5.12kWh داشته باشد. در این مدل از دستگاههای تزریق، دمای تزریق بالاتر، زمان خنکشو بیشتر بوده و بدلیل امکان نشتی روغن برای محیطهای بهداشتی مناسب نیستند.
همچنین دستگاههای تزریق پلاستیک پر سر و صداتر و کم دقتتر از دستگاههای برقی میباشند. اما با افزایش نیروی قفل گیره و پیشرفت سیستمهای کنترلی، دقت و بازدهی دستگاههای هیدرولیکی نیز بهبود یافته است.
دستگاه تزریق پلاستیک تمام برقی
دستگاههای تزریق پلاستیک تمام برقی به عنوان پیشرفتهترین دستگاههای تزریق پلاستیک شناخته میشوند و در مقایسه با سایر دستگاهها دارای ویژگیهای عملکردی منحصر به فرد میباشند.حرکات خطی رفت و برگشتی در دستگاه تزریق پلاستیک برقی توسط ترکیب سروو موتور و بال اسکرو انجام میشود. حرکات دورانی نیز مستقیماً به وسیله سروو موتور و یا با کمک گیربکس تامین میشوند.
از جمله مهمترین مزایای دستگاه تزریق پلاستیک تمام برقی میتوان به دقت بینظیر، سرعت بالا و پاکیزگی به دلیل عدم وجود روغن هیدرولیک به عنوان مادهای آلاینده اشاره کرد.
مزایا دستگاه تزریق پلاستیک برقی:
از آنجایی که هیچگونه آلودگی روغن وجود ندارد، دستگاههای تزریق برقی برای محیطهای بهداشتی بسیار مناسب هستند. بدلیل دقت بالای این دستگاهها، برای تولید قطعات کوچک تا متوسط پزشکی همانند سرنگ و ظرفهای پتری (Petri dishes) ایدهآل میباشند. سایر مزایا عبارتند از:
- دقت و تکرارپذیری بسیار بالا با کاهش نرخ خرابی
- تولید پاکیزهتر بدون خطر نشتی مایعاتی چون روغن
- زمان خرابی کمتر در مقایسه با دستگاههای هیدرولیکی
- کاهش مصرف انرژی 30% تا 70%
- کارکرد کم صدا، کاهش صدای موتور زیر 70dB
- سرعت تزریق بالاتر تا 800mm/sec و حرکت گیره سریعتر
- زمان روشن شدن کمتر و زمان سیکل سریعتر تا 20%
- هزینه واحد پایین با کاهش هدر رفت مواد
- به هیچ ماده مصرفی مانند روغن جهت جایگزینی و تمیز کردن نیاز ندارد.
- نیاز به مصرف برق کمتر که تولید با هزینه کمتر را بدنبال دارد.
نقاط ضعف دستگاه تزریق پلاستیک برقی:
اگرچه دستگاههای تزریق برقی سریعتر، تمیزتر و کم مصرفتر میباشند، اما آنها نمیتوانند نیروی قفل گیره تولید شده توسط دستگاههای هیدرولیکی را ایجاد کرده و ضمنا هزینه اولیه بالاتری نیز برای مشتری دارند. گیره این دستگاهها مکانیزم بازویی هستند که توسط ball-screw به حرکت در میآید، قطعاتی که امکان سایش در آن ها وجود داشته و هزینه تعویض بالایی دارند. بدلیل ارائه دقت بسیار بالای دستگاههای برقی، نقاط ضعف اشاره شده کمتر میتواند موجب فراموشی این مدل در مقایسه با دستگاههای هیدرولیکی شود.
دستگاه تزریق پلاستیک هیبریدی
دستگاه تزریق پلاستیک هیبریدی، تلفیقی از دستگاه تزریق پلاستیک برقی و هیدرولیکی است که در آن دقت و سرعت عملگرهای برقی با قدرت بالای عملگرهای هیدرولیکی ترکیب شده است. دستگاههای هیبریدی بسیار متنوع هستند و عموماً بر حسب نیاز تولیدکنندگان، به صورت سفارشی طراحی و ساخته میشوند.
مزایا دستگاه تزریق پلاستیک هیبریدی:
دستگاه تزریق پلاستیک هیبرید مناسب برای یک فرآیند بهینه، کم مصرف و طولانی مدت بدون نیازمندی خاص میباشد که این امر منجر به بازگشت سرمایه سریعتر میشود.
برخی از مزایای خاص این دستگاههای عبارتند از:
- تنظیمات پیوسته بواسطه بکارگیری پمپ سروو
- تنوع طراحی محصول
- هزینه اولیه متوسط هر سه دستگاه (هیدرولیکی، برقی و هیبریدی)، اما میتواند بیشترین سود را در طول زمان داشته باشد.
- سیستم کنترل حلقه بسته با سرعت پاسخدهی سریعتر
- دمای پایینتر موجب زمان خنکشو کمتر شده و عمر روغن و دستگاه را بیشتر میکند.
- زمان سریعتر به ROI بدلیل بازدهیهای اشاره شده
نقاط ضعف دستگاه تزریق پلاستیک هیبریدی:
از آنجایی که تمامی دستگاههای هیبرید متفاوت هستند، امکان خوراندن و انتخاب گیره مناسب برای تولید قطعه در صورت جایگزینی دستگاه سخت خواهد بود. همچنین در صورت هر گونه تعمیرات ضروری در دستگاه هیبرید، تعمیرکار باید دانش هر دو دستگاه هیدرولیکی و برقی را داشته باشد.
روش کار با دستگاه تزریق پلاستیک
نخستین گام برای شروع کار با دستگاه تزریق پلاستیک، آماده سازی قالب است، در این مرحله نصب اصولی با قالب بر روی صفحات گیره دستگاه از اهمیت زیادی برخوردار است و باید رعایت مسائل ایمنی با استفاده از کلمپ یا روبند مناسب انجام گیرد.
قالب در فرایند تزریق پلاستیک کمابیش اهمیتی برابر با دستگاه تزریق پلاستیک دارد و کیفیت تولید قطعات پلاستیکی را مستقیماً تحت تاثیر قرار میدهد.
در عمومی ترین حالت یک قالب تزریق پلاستیک از دو بخش ثابت و متحرک تشکیل میشود که در اغلب مواقع بخش حفره قالب یا کویته در قسمت ثابت و بخش مغزی یا سنبه قالب در قسمت متحرک قالب قرار میگیرد. فضای خالی میان کویته قالب و سنبه جایی است که مواد پلاستیکی پس از ذوب و تزریق وارد آن میشوند و به فرم قطعه مورد نظر منجمد میشوند. برای تولید هر قطعه پلاستیکی بایستی قالبی اختصاصی مطابق با شکل هندسی و ابعاد آن قطعه ساخته شود.
پس از نصب قالب در مرحله بعد قیف دستگاه تزریق پلاستیک با مواد اولیه تغذیه میشود که این کار هم به صورت دستی و توسط یک کارگر و هم به صورت خودکار با استفاده از دستگاه موادکش اتوماتیک انجام میشود.
مرحله بعدی که باید انجام گیرد، تست قالب و انجام تنظیمات اولیه است. در این مرحله پارامترهایی مانند سرعت تزریق، فشار تزریق، دمای بارگیری و سرعت و فشار حرکت گیره بر اساس تجربه و یا با حدس تعیین میشوند. سپس با ادامه کار دستگاه و بررسی نمونه قطعات تولیدی، پارامترها مورد بازنگری و اصلاح قرار میگیرند تا جایی که مقادیر بهینه آنها برای تولید قطعه مورد نظر تعیین شود. پس از این مرحله دستگاه تزریق پلاستیک آماده کار است و میتواند به صورت اتوماتیک به تولید قطعه بپردازد.
روش کارکرد دستگاه تزریق پلاستیک
فرایند تولید به روش تزریق پلاستیک طی چرخهای تکرار شونده انجام میگیرد که سیکل تولید نامیده میشود. زمانی که برای اولین بار مواد به درون قیف ریخته شده و مواد در داخل سیلندر بارگیری و ذوب شده باشند، نخستین مرحله از سیکل تولید آغاز میشود. در این مرحله ماردون به جلو حرکت کرده و مکانیزم شیر یک طرفهای که در نوک ماردون قرار گرفته است باعث میشود تا مواد به سمت جلو حرکت کرده و از طریق نازل تزریق به درون قالب تزریق شوند. به دلیل چگالی بالای پلاستیک مذاب، پر شدن فضای قالب نیاز به فشار بسیار بالایی دارد که میتواند به بیش از 2 هزار برابر فشار اتمسفر نیز برسد.
پس از پر شدن قالب مرحله دوم از سیکل تولید با نام اتوکشی آغاز میشود که برای جلوگیری از تغییر شکل ناشی از انقباض مواد به هنگام انجماد در قالب ضروری است. در مرحله اتوکشی ماردون همچنان با نیرویی در حدود 70% نیروی صرف شده در زمان تزریق مواد را تحت فشار نگاه میدارد و مدت زمان اتوکشی معمولاً کوتاه و اغلب کمتر از 2 ثانیه است. دستیابی به تلرانسهای هندسی و ابعادی مورد انتظار علاوه بر کیفیت ساخت قالب، به تنظیمات اتوکشی نیز بستگی دارد.
مواد مذاب بلافاصله پس از تزریق و در تماس با سطح سرد قالب، دمای خود را از دست میدهند، اما تا رسیدن به حدی از دما که در اثر خروج از قالب دچار تغیر شکل نشوند لازم است که در قالب باقی بمانند و سرد شوند. گردش مداوم آب سرد در قالب باعث میشود تا دمای قالب پایین نگه داشته شود و انتقال حرارت مورد نیاز برای انجماد قطعه فراهم شود. مرحله خنک سازی به ابعاد و جنس قطعه بستگی دارد و معمولاً طولانی ترین بخش سیکل تولید محسوب میشود.
فرایند خنک شدن و مدت زمان انجام آن نیز تاثیر مستقیمی بر کیفیت و وضعیت هندسی و ابعادی قطعه خواهد داشت. چنانچه خنک شدن بسیار سریع اتفاق بیفتد، قطعه دچار تابیدگی میشود. در مقابل اگر خنک شدن کند انجام شود باعث طولانی شدن سیکل تولید و کاهش بازدهی اقتصادی تولید قطعه خواهد شد.
پس از پایان مرحله اتوکشی و به موازات خنک سازی قطعه، مرحله بارگیری آغاز میشود که شامل هدایت مواد از قیف به سمت جلو سیلندر است. بارگیری مواد به وسیله گردش ماردون انجام میشود و در اثر گرمای هیترهای سیلندر تزریق و نیروی برشی ایجاد شده از گردش ماردون، مواد ذوب میشوند.
پس از پایان مرحله بارگیری، چنانچه دمای قطعه به میزان مناسب کاهش یافته باشد، مرحله بعدی سیکل تولید آغاز میشود، در غیر این صورت دستگاه در وضعیت غیر فعال باقی خواهد ماند تا مرحله خنک سازی به پایان برسد. مرحله بعدی شامل پران قطعه است که با باز شدن گیره و فاصله گرفتن بخش ثابت و متحرک قالب از یکدیگر آغاز میشود و در ادامه با فعال شدن مکانیزم پران، قطعه تولید شده از قالب جدا میشود.
سپس در گیره بسته شده و با چفت شدن دو نیمه قالب و آماده شدن برای تزریق مجدد مواد و تولید قطعه جدید، یک سیکل تولید به پایان میرسد.
اصول طراحی و تولید قالب تزریق پلاستیک
توجه داشته باشید پیش نیاز تزریق پلاستیک بدون نقص و ایراد، طراحی یک قالب بدون اشکال است. به همین دلیل برخی از نکات در زمان طراحی یا سفارش ساخت قالب باید مورد توجه قرار گیرند. یکی از مهم ترین نکات در طراحی و ساخت قالب تزریق پلاستیک، آگاهی از رفتار مواد پلیمری در زمان ذوب و انجماد است.
نکته دیگری که توجه به آن حائز اهمیت است، در نظر گرفتن تواناییهای دستگاه تزریق پلاستیک است. چنانچه محور حرکت گیره دستگاه تزریق پلاستیک را معیار قرار دهیم، میتوان دستگاههای تزریق پلاستیک را در دو دسته عمودی و افقی قرار تقسیم بندی کرد که هر کدام ویژگیها و قابلیتهای خاص خود را دارند.
نوع سیستم قدرت دستگاه اعم از هیدرولیکی، تمام برقی و یا هیبریدی و همچنین برند دستگاه تزریق از جمله به مواردی هستند که در هنگام طراحی قالب نباید نسبت به آنها بیتفاوت باشید. اطلاع از تواناییهای دستگاه تزریق پلاستیک مانند حداکثر وزن تزریق، نیروی گیره، فاصله بین تایبارها و مقدار بازشو گیره میتواند نتیجه کار طراحی قالب را تا حد زیادی تحت تاثیر قرار دهد.
انتخاب سیستم راهگاه مناسب و نوع و موقعیت گیت تزریق از دیگر موارد مهم در طراحی قالب تزریق پلاستیک به شمار میرود. در بسیاری از موارد مزایای سیستم راهگاه گرم یا هات رانر به هزینه آن میارزد و با افزایش بازدهی تولید، کاهش زمان سیکل تولید و حذف عملیات جداسازی راهگاه میتواند صرفه اقتصادی قابل توجهی را به همراه داشته باشد.
مهم ترین مواد اولیه تزریق پلاستیک
· Nylon
نایلون یا پلی آمید (Polyamide) یکی از پلیمرهای پر کاربرد در تزریق پلاستیک است و برای ساخت بسیاری از وسایل مربوط به اتومبیلها و قطعات خودرو مانند چرخدنده، بلبرینگ هرزگرد، منیفولد هوا، پروانه رادیاتور و قاب سنسور مپ استفاده میشود. پلی آمید الیاف دار یا بدون الیاف دارای مزایا و ویژگیهای قابل توجهی شامل مقاومت به ضربه، استحکام فوق العاده، ضریب اصطکاک پایین، قابلیت تحمل دمای بالا و مقاومت شیمیایی عالی است. نایلون در برابر جذب رطوبت آسیب پذیر است و خواص مکانیکی آن با از قرار گرفتن در معرض رطوبت آسیب میبیند.
· PE
پلی اتیلن (Polyethylene) پر کاربرد ترین ماده اولیه تزریق پلاستیک است که معمولاً در دو گروه کلی HDPE و LDPE یا پلی اتیلن سنگین و پلی اتیلن سبک دسته بندی و عرضه میشود. پلی اتیلن انعطاف پذیری و مقاومت شیمیایی بسیار بالایی دارد و به لحاظ قیمت یکی از ارزان ترین مواد اولیه تزریقی است. از پلی اتیلن در ساخت انواع درب بطری، بطری شامپو، مایع ظرفشویی، انواع دبه و گالن پلاستیکی، سطل پلاستیکی و لوازم خانگی استفاده میشود.
· POM
پلی اکسی متیلن (Polyoxymethylene) که بیشتر با نام استال یا پلی استال شناخته میشود مادهای است با چقرمگی و استحکام بسیار بالا که حتی در دمای پایین نیز قابلیت مقاومت به ضربه دارد. بر خلاف پلی آمید به رطوبت حساسیت ندارد و به دلیل پایداری ابعادی و مقاومت به سایشی که دارد از آن برای تولید انواع چرخدندههای پلاستیکی استفاده میشود.
· PC
پلی کربنات (POLYCARBONATE) یکی از پلاستیکهای شفاف و دارای مقاومت به ضربه است که به دلیل ویژگیهای اپتیکی منحصر به فردی که دارد در ساخت چراغ عقب و جلو خودرو، حباب لامپ LED، عینک ایمنی و لنز پلاستیکی کاربرد گستردهای دارد. تزریق پلی کربنات نیازمند استفاده از سیلندر و ماردون مخصوص و گازگیر است.
· ABS
ای بی اس (Acrylonitrile butadiene styrene/ABS) یکی از مهم ترین ترموپلاستیکها برای تزریق پلاستیک و تولید قطعات لوازم خانگی است و به دلیل پایداری ابعادی بالا، قابلیت جوشکاری، براق بودن و قابلیت آبکاری بالای آن بسیاری از لوازم خانگی، لوازم برقی و قطعات خودرو از آن ساخته میشوند.
· ABS/PC
یک آلیاژ پلیمری بسیار پر کاربرد در تزریق پلاستیک است که از ترکیب پلی کربنات و ای بی اس ساخته میشود و برای ساخت قطعات بزرگ مانند لوازم خانگ، قطعات بدنه یخچال و فریز، سپر خودرو و … استفاده میشود. این ترکیب در برابر گرما و ضربه دوام و سختی بسیار بالایی دارد.
· PS
کریستال یا پلی استایرن (Polystyrene) یک پلیمر شفاف اما شکننده است که به دلیل قیمت پایین و مقرون به صرفه، کاربردی وسیع در ساخت لیوان یکبار مصرف، قاشق و چنگال یکبار مصرف، تجهیزات پزشکی و لوازم مصرفی آزمایشگاهی دارد.
· PP
پلی پروپیلن (Polypropylene) پس از پلی اتیلن، پر مصرف ترین پلیمر در تولید قطعات تزریقی است. مقاومت شیمیایی بالا، انعطاف پذیری بی نظیر، استحکام مناسب، چقرمگی و مقاومت به ضربه عالی پلی پروپیلن در کنار شفافیت و قیمت مناسبی که دارد باعث شده تا محصولات متنوعی مانند انواع لوازم خانگی، صندلی پلاستیکی، سطل، لگن، سبد پلاستیکی، پالت، سطل زباله بیمارستانی، ظروف پلاستیکی مایکروویو، سرنگ و قطعات تجهیزات پزشکی از پلی پروپیلن ساخته شوند.
· PBT
پی بی تی (Polybutylene Terephthalate) پلیمری است که استحکام، چقرمگی و پایداری ابعادی بالایی دارد. کامپاند پی بی تی با الیاف شیشه ترکیبی است که در ساخت قطعات خودرو و لوازم و تجهیزات برقی مانند بدنه لامپ و کلید و پریزهای صنعتی کاربرد دارد.
· PET
پلاستیک پت یا PET (Polyethylene Terephthalate) پلیمری هم خانواده با PBT است و یکی از شفاف ترین پلیمرهای تزریقی محسوب میشود. قابلیت قالبگیری بادی، مقاومت شیمیایی بالا به همراه مطلوبیت خواص مکانیکی از قبیل استحکام، چقرمگی و مقاومت به خزش باعث محبوبیت PET در ساخت پریفرم انواع بطری، بطری نوشابه، بطری روغن مایع، قوطی قرص و … شده است.
مزایای دستگاه تزریق پلاستیک
- تزریق پلاستیک ساده ترین روش برای تولید انبوه قطعات پلاستیکی با کیفیت یکسان است.
- دستگاه تزریق به نگهداری و تعمیر بسیار کمی احتیاج دارند و با رعایت صحیح دستور العملهای استفاده از دستگاه تزریق پلاستیک، برای ده ها سال قابل استفاده خواهد بود.
- تنوع بسیار گستردهای دارد و برای کاربردهای خاص قابل سفارشی سازی است.
- دستگاههای تزریق پلاستیک به صورت اتوماتیک کنترل میشوند و فرآیند آنها نیازی به نظارت ندارد.
- این دستگاهها فضای نسبتاً کمی را اشغال میکنند و طریقه کارکردن با آنها نیز بسیار راحت است.
- ضایعات تزریق پلاستیک مجدداً قابل استفاده هستند.
- قطعات تولید شده با دستگاه تزریق پلاستیک معمولاً محصول نهایی بوده و نیازی به عملیات ثانویه تولید وجود ندارد.
- قطعات یدکی دستگاه تزریق پلاستیک به آسانی در بازار پیدا میشود.
آشنایی با ۳ نوع دستگاه تزریق پلاستیک از نگاهی دیگر
امروزه ما در زندگی روزمره خود از پلاستیک ها استفاده های متنوعی می کنیم و باید بدانیم که برای تولید این پلاستیک ها از قالب ها و انواع دستگاه تزریق پلاستیک استفاده می شود. برای افرادی که در حوزه تولید پلاستیک فعالیت می کنند ضروری است که انواع دستگاه های تزریق را بشناسند، مزایا و معایب آن ها را بررسی کنند و بهترین گزینه را برای تولید قطعات پلاستیکی در نظر بگیرند. اگر شما به مبحث تولید این مواد پرکاربرد علاقه مند هستید، در ادامه این مقاله همراه ما باشید.
روش تزریق پلاستیک
مواد پلاستیکی به طور خام و بدون قالب گیری ارزش و کاربرد خاصی ندارند. به همین علت برای بهینه سازی کاربرد این مواد، باید آن ها را قالب گیری کرد. قالب گیری به روش تزریق از محبوب ترین روش های قالب گیری پلاستیک ها است. مهم ترین دلیل محبوبیت این روش تولید انبوه قطعات پلاستیکی است. طیف گسترده ای از محصولات پلاستیکی با استفاده از این روش قالب گیری ساخته می شوند که از لحاظ ابعاد و کاربرد با هم متفاوت هستند. برای انجام قالب گیری از انواع دستگاه تزریق پلاستیک استفاده می شود که در ادامه با سازوکار آن ها آشنا می شویم.
معرفی دستگاه تزریق پلاستیک (Plastic Injection Machine)
دستگاه تزریق پلاستیک دستگاهی است که قالب گیری تزریقی توسط آن انجام می شود. ما برای قالب گیری تزریقی انواع دستگاه های تزریق پلاستیک را داریم. لبه دستگاه قالب گیری تزریقی به صورت افقی و عمودی بسته می شود. اکثر دستگاه های تزریق پلاستیک افقی بسته می شوند. دستگاه تزریقی که به صورت عمودی بسته می شود برای ساخت برخی سازه ها کاربرد دارد. برای بسته شدن دستگاه معمولا از گیره های دستی استفاده می شود. با این حال در برخی از دستگاه ها که نیاز به تغییر سریع ابزار دارند، گیره های هیدرولیکی یا مغناطیسی به کار می روند.
دستگاه تزریق پلاستیک دو بخش کلی دارد:
- گیره دستگاه: باز و بسته کردن قالب و بیرون پرتاب کردن قطعات به عهده این بخش است.
- قسمت تزریق: عملیات تزریق مذاب و قالب گیری نیز در این بخش از دستگاه تزریق انجام می شود.
حال که با سازوکار دستگاه و بخش های آن آشنا شدیم، به معرفی و بررسی انواع دستگاه تزریق پلاستیک می پردازیم.
انواع دستگاه تزریق پلاستیک
در این بخش به معرفی انواع دستگاه تزریق پلاستیک می پردازیم تا شما با مزایا و معایب آن ها آشنا شوید. به طور کلی دستگاه های تزریق به سه نوع زیر تقسیم بندی می شوند:
- هیدرولیکی
- برقی
- هیبریدی
آشنایی با دستگاه تزریق هیدرولیکی
در این نوع دستگاه از انواع دستگاه تزریق پلاستیک، از جک های هیدرولیکی برای قفل شدن دو قالب استفاده می شود. پس از آن مواد مذاب پلاستیکی به درون حفره های قالب تزریق می شوند وبعد از خنک شدن پلاستیک تزریق شده، دو قالب از هم جدا و قطعه خارج می شود. برای این که قالب هنگام اعمال فشار باز نشود، واحد گیره دستگاه هنگام تزریق مواد باید توانایی تحمل فشار را داشته باشد.
برای قطعاتی که جداره نازکی دارند، نیروی قفل دستگاه باید حدود 3 تا 4 تن بر اینچ مربع باشد؛ اما برای قطعاتی که ضخیم تر هستند نیروی قفل باید بیشتر باشد. متوسط نیروی قفل دستگاه های تزریق هیدرولیکی 8000 تن است و این دستگاه یکی از مهم ترین دستگاه ها در صنایع خودرو محسوب می شود. به طور کلی عمدتا برای ساخت قطعات بزرگ و سنگین پلاستیکی از این نوع دستگاه تزریق استفاده می شود.
مزایای به کار گیری این نوع از انواع دستگاه تزریق پلاستیک عبارتند از:
- نیروی قفل بالا برای قطعات سنگین و بزرگ
- سرعت تزریق بالاتر
- مقاومت سایشی بالا
- حجم تزریق بیشتر
- هزینه اولیه کمتر
- دسترسی آسان به قطعات یدکی دستگاه
- آسان بودن روش استفاده
- در دسترس بودن قطعات اصلی دستگاه در صورت خراب شدن
البته این نوع دستگاه ها معایبی هم دارند که هنگام انتخاب باید به آن ها توجه کرد.
از جمله معایب این دستگاه عبارتند از:
- مصرف انرژی بالا
- دمای تزریق بالا
- زمان طولانی برای خنک شدن
- نشتی روغن از دستگاه
- سر و صدای زیاد
آشنایی با دستگاه تزریق برقی
دستگاه تزریق برقی یکی دیگر از انواع دستگاه تزریق پلاستیک است که دقت بالایی دارد. موتور این دستگاه ها سرعت بالایی دارد و دیجیتالی کنترل می شود. تفاوت این دستگاه با نوع هیدرولیکی آن در سرعت، دقت بالا و مصرف انرژی کمتر است. همچنین امکان تولید انبوه از یک قطعه مشخص در این دستگاه وجود دارد. وقتی که برنامه ریزی دستگاه تزریق برقی انجام می شود، کنترلر های دیجیتالی فرآیند دستگاه را کنترل می کنند و به همین علت به نیروی کار کمتری نیاز است، هزینه ها کاهش می یابند و سوددهی افزایش پیدا می کند. دستگاه های تزریق برقی برای تولید محصولات پلاستیکی با ابعاد کوچک مثل محصولات پزشکی چون سرنگ و… مناسب هستند.
از جمله مزایای این دستگاه ها می توان موارد زیر را نام برد:
- دقت و تکرارپذیری بالا
- بدون نشتی روغن
- زمان خرابی کمتر
- کاهش مصرف انرژی و برق
- صدای کم
- سرعت تزریق بالاتر
- هزینه پایین به علت کاهش دورریز مواد
البته همان طور که برای دستگاه هیدرولیکی نیز اشاره کردیم، دستگاه تزریق برقی نیز معایبی دارد:
- عدم داشتن نیروی قفل بالا برای تولید محصولات بزرگ تر
- هزینه بیشتر مواد اولیه
- امکان سایش قطعات
- هزینه بالای تعمیرات
آشنایی با دستگاه تزریق هیبریدی
دستگاه تزریق هیبریدی آخرین نوع از انواع دستگاه تزریق پلاستیک است که می توان گفت ترکیبی از هر دو دستگاه هیدرولیکی و برقی می باشد. این دستگاه دارای نیروی قفل بالایی مثل دستگاه هیدرولیکی و دقت و تکرارپذیری بالا و مصرف انرژی کمتر مشابه دستگاه های برقی است. به همین دلیل دستگاه هیبریدی گزینه ای عالی برای تولید همه قطعات پلاستیکی با ابعاد مختلف است.
از مزایای دستگاه هیبریدی می توان به موارد زیر اشاره کرد:
- تنوع در طراحی قطعات مختلف
- سیستم کنترل حلقه بسته و افزایش سرعت پاسخ دهی
- دمای کمتر برای خنک شدن
- افزایش طول عمر دستگاه
دستگاه هیبریدی نیز همچون سایرین معایبی دارد که حائز اهمیت هستند.
از جمله این معایب می توان موارد زیر را نام برد:
- انتخاب گیره های مختلف برای قطعات مختلف
- تعمیرات سخت به علت ترکیبی از هردو دستگاه فوق
- هزینه تعمیرات بالا